汽輪發(fā)電機(jī)組振動現(xiàn)場診斷
引起汽輪發(fā)電機(jī)組振動的原因往往較為復(fù)雜,因素較多。例如,一些振動不僅與質(zhì)量不平衡、不對中等旋轉(zhuǎn)機(jī)械本身的因素有關(guān),而且與運(yùn)行中電氣、熱膨脹、流體等因素有關(guān),有些還與結(jié)構(gòu)剛度和安裝質(zhì)量有關(guān)。因此需要進(jìn)行一些有關(guān)的振動試驗(yàn)來確定引起振動的原因。
The causes of vibration in steam turbine generator sets are often complex and have many factors. For example, some vibrations are not only related to factors such as mass imbalance and misalignment of rotating machinery itself, but also to factors such as electrical, thermal expansion, and fluid during operation. Some are also related to structural stiffness and installation quality. Therefore, it is necessary to conduct some relevant vibration tests to determine the cause of the vibration.
對于轉(zhuǎn)速的升降速振動試驗(yàn)
Vibration test for speed increase and decrease
該實(shí)驗(yàn)的目的是確定機(jī)組實(shí)際的軸系臨界轉(zhuǎn)速和相位的振動值。由于制造廠商提供的都是計算臨界轉(zhuǎn)速,在計算中有關(guān)參數(shù)的模擬可能與實(shí)際機(jī)組本身和其安裝條件有些偏差,故計算結(jié)果和實(shí)際值會有一定的誤差。機(jī)組的臨界轉(zhuǎn)速應(yīng)以實(shí)測結(jié)果為準(zhǔn)。根據(jù)過臨界轉(zhuǎn)速時的振動值大小,也可以判斷轉(zhuǎn)子各階振型的平衡狀況。
The purpose of this experiment is to determine the actual critical speed and phase vibration values of the shaft system of the unit. Due to the fact that manufacturers only provide critical speed calculations, the simulation of relevant parameters in the calculation may deviate from the actual unit itself and its installation conditions, resulting in certain errors between the calculation results and the actual values. The critical speed of the unit should be based on the measured results. Based on the magnitude of the vibration value at the critical speed, the balance status of each vibration mode of the rotor can also be determined.
該實(shí)驗(yàn)的另一個目的是可以確定轉(zhuǎn)子是否發(fā)生熱彎曲。如果冷態(tài)下機(jī)組啟動過程中過臨界轉(zhuǎn)速時的振動值不大,但在帶負(fù)荷運(yùn)行一段時間后快速降負(fù)荷并解列打閘停機(jī)過程中臨界轉(zhuǎn)速下振動增大許多時,則可以作為判斷轉(zhuǎn)子產(chǎn)生了熱彎曲的因素之一。
Another purpose of this experiment is to determine whether the rotor has undergone thermal bending. If the vibration value at the critical speed during the cold start process of the unit is not significant, but after running under load for a period of time, the load is quickly reduced and the vibration at the critical speed increases significantly during the trip and shutdown process, it can be used as one of the factors that determine the thermal bending of the rotor.
發(fā)電機(jī)勵磁電流試驗(yàn)
Generator excitation current test
發(fā)電機(jī)勵磁電流試驗(yàn)的目的是判斷機(jī)組振動原因,是來自電磁方面還是機(jī)械方面,電磁方面的原因可分為兩種:
The purpose of generator excitation current test is to determine the cause of unit vibration, whether it comes from electromagnetic or mechanical aspects. The electromagnetic reasons can be divided into two types:
一是,由于純電磁激振力引起的振動(如發(fā)電機(jī)轉(zhuǎn)子線圈匝間短路以及轉(zhuǎn)子與定子間的空氣不均勻引起的激振力);
One is the vibration caused by pure electromagnetic excitation force (such as the excitation force caused by the inter turn short circuit of the generator rotor coil and the uneven air between the rotor and stator);
二是,由于電方面的原因引起的,發(fā)電機(jī)受熱不均的熱彎曲而引起的振動。
The second is the vibration caused by uneven thermal bending of the generator due to electrical reasons.
后者由于轉(zhuǎn)子熱慣性,其振動值的增大在時間上較勵磁變化滯后,通常只有在發(fā)電機(jī)轉(zhuǎn)子勵磁電流有較大幅度變化時,振動才有明顯改變。勵磁電流試驗(yàn)是在機(jī)組帶上一定負(fù)荷時,保持該負(fù)荷不變而增大發(fā)電機(jī)轉(zhuǎn)子勵磁電流(降低功率因素)的條件下進(jìn)行的,發(fā)電機(jī)轉(zhuǎn)子勵磁電流的變化范圍是,以不超過其額定值為限。通常隨著勵磁電流增加,振動值也隨之增大。如試驗(yàn)曲線呈光滑上升形狀,則說明振動直接與勵磁電流有關(guān),是純電氣原因造成的。如振幅增加呈階梯形,即振動不立即隨勵磁電流的增加而增大,而是到一定時間階躍增加,則振動是因轉(zhuǎn)子熱彎曲變形增大引起的,通常的原因是轉(zhuǎn)子冷卻通風(fēng)道開孔不正確或灰塵、雜物的不均勻堵塞、線圈膨脹受阻等。
Due to the thermal inertia of the rotor, the increase of its vibration value lags behind the excitation change in time. Usually, only when there is a significant change in the excitation current of the generator rotor, does the vibration change significantly. The excitation current test is conducted under the condition of increasing the excitation current of the generator rotor (reducing power factor) while maintaining a certain load on the unit. The variation range of the excitation current of the generator rotor is limited to its rated value. Usually, as the excitation current increases, the vibration value also increases. If the test curve shows a smooth rising shape, it indicates that the vibration is directly related to the excitation current and is caused solely by electrical reasons. If the amplitude increases in a stepped shape, that is, the vibration does not immediately increase with the increase of excitation current, but increases step by step at a certain time, then the vibration is caused by the increase in thermal bending deformation of the rotor. The usual reasons are incorrect opening of the rotor cooling ventilation duct, uneven blockage of dust and debris, and obstruction of coil expansion.
并網(wǎng)前后振動變化。如果并網(wǎng)前后振動變化較大,說明轉(zhuǎn)子上存在不平衡電磁力的作用。例如,電動機(jī)出現(xiàn)故障后,可以采用“斷電速查”法,根據(jù)斷電瞬間振動的變化情況判斷電氣缺陷情況。
Vibration changes before and after grid connection. If the vibration changes significantly before and after grid connection, it indicates the presence of unbalanced electromagnetic force on the rotor. For example, after a motor malfunction occurs, the "power outage quick check" method can be used to determine the electrical defect situation based on the changes in vibration at the moment of power outage.
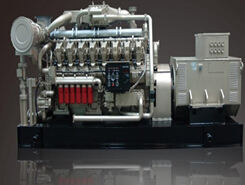
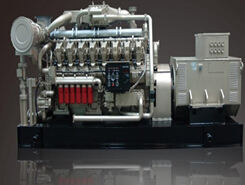
勵磁電流變化后,振動隨即變化,兩者之間沒有滯后。這種現(xiàn)象說明振動主要是由于電氣缺陷引起的。發(fā)電機(jī)轉(zhuǎn)子線圈出現(xiàn)匝間短路后,振動變化將以基頻為主。發(fā)電機(jī)轉(zhuǎn)子與靜子間的空氣間隙不均勻,將會誘發(fā)較大的二倍頻振動,轉(zhuǎn)子振動增大的同時,靜子振動一般也會增大。
After the excitation current changes, the vibration changes immediately, and there is no lag between the two. This phenomenon indicates that vibration is mainly caused by electrical defects. After the inter turn short circuit occurs in the generator rotor coil, the vibration change will be mainly based on the fundamental frequency. The uneven air gap between the generator rotor and stator will induce significant second harmonic vibration. As the rotor vibration increases, the stator vibration generally also increases.
勵磁電流變化后,振動逐漸變化,一段時間后才能穩(wěn)定下來,振動變化滯后于勵磁電流變化。這種現(xiàn)象說明振動主要是由于熱變形引起的??赡艿脑蛴校涸验g短路誘發(fā)的轉(zhuǎn)子部件非對稱熱變形,通風(fēng)孔堵塞、冷卻水量不均勻等誘發(fā)的轉(zhuǎn)子冷卻不均勻以及部件松動或膨脹受阻等。
After the excitation current changes, the vibration gradually changes and stabilizes after a period of time. The vibration changes lag behind the excitation current changes. This phenomenon indicates that vibration is mainly caused by thermal deformation. Possible reasons include asymmetric thermal deformation of rotor components caused by inter turn short circuits, uneven cooling of the rotor caused by blocked ventilation holes, uneven cooling water volume, and looseness or expansion of components.
圖片
picture
發(fā)電機(jī)冷卻介質(zhì)溫度試驗(yàn)
Generator cooling medium temperature test
當(dāng)發(fā)電機(jī)轉(zhuǎn)軸存在不對稱冷卻時,發(fā)電機(jī)轉(zhuǎn)子會發(fā)生熱彎曲,引起振動增大。因此,通過改變冷卻介質(zhì)的溫度,可以判斷有無不對稱冷卻。對于水冷發(fā)電機(jī)可采用改變冷卻水溫試驗(yàn),而對于氫冷發(fā)電機(jī)可采用改變冷卻氫溫試驗(yàn),觀察其變化對振動發(fā)展的影響。雙流式氫冷系統(tǒng),可以單獨(dú)改變發(fā)電機(jī)某一端氫冷器的出口氫溫,有助于判斷不對稱冷卻發(fā)生在轉(zhuǎn)子的哪一端。通常在存在不對稱冷卻故障時,冷卻介質(zhì)溫度越高,振動越小。
When there is asymmetric cooling of the generator shaft, the generator rotor will undergo thermal bending, causing increased vibration. Therefore, by changing the temperature of the cooling medium, it is possible to determine whether there is asymmetric cooling. For water-cooled generators, changing the cooling water temperature test can be used, while for hydrogen cooled generators, changing the cooling hydrogen temperature test can be used to observe the impact of its changes on vibration development. The dual flow hydrogen cooling system can independently change the outlet hydrogen temperature of the hydrogen cooler at one end of the generator, which helps to determine which end of the rotor asymmetric cooling occurs. Usually, in the presence of asymmetric cooling faults, the higher the temperature of the cooling medium, the smaller the vibration.
負(fù)荷試驗(yàn)
Load test
負(fù)荷改變后,流量、溫度、壓力、聯(lián)軸器傳遞扭矩、汽流激振力、汽缸膨脹、軸承標(biāo)高等都會發(fā)生變化,從而有可能影響機(jī)組振動。負(fù)荷試驗(yàn)可以在空負(fù)荷、中間負(fù)荷和滿負(fù)荷三種狀態(tài)下進(jìn)行。負(fù)荷改變后,應(yīng)立即測量振動。然后,保持負(fù)荷不變,穩(wěn)定一段時間或等振動不變后再次測取振動值。負(fù)荷變化后,一般需要穩(wěn)定30分鐘以上。
After the load changes, the flow rate, temperature, pressure, torque transmitted by the coupling, steam flow excitation force, cylinder expansion, bearing elevation, etc. will all change, which may affect the vibration of the unit. The load test can be conducted under three states: no-load, intermediate load, and full load. After the load changes, the vibration should be measured immediately. Then, keep the load constant, stabilize for a period of time, or measure the vibration value again after the vibration remains unchanged. After a load change, it usually needs to stabilize for more than 30 minutes.
負(fù)荷試驗(yàn)的目的是判斷機(jī)組負(fù)荷變化過程中,汽輪機(jī)的機(jī)械狀態(tài)和熱狀態(tài)的變化對振動的影響。當(dāng)機(jī)組負(fù)荷變化時,一方面汽輪機(jī)經(jīng)聯(lián)軸節(jié)傳遞到發(fā)電機(jī)的扭矩立即會發(fā)生變化,如果聯(lián)軸節(jié)有缺陷,則機(jī)組的振動狀態(tài)也會立即發(fā)生變化。另一方面,因流過汽輪機(jī)的蒸汽流量變化,會引起汽缸內(nèi)蒸汽壓力和溫度分布的變化,也即汽輪機(jī)汽缸、轉(zhuǎn)子和軸承座的熱膨脹要相應(yīng)改變。如果此時汽缸出現(xiàn)不均勻變形而使轉(zhuǎn)子不正,導(dǎo)致軸承不能正常工作或汽缸滑銷系統(tǒng)卡澀等缺陷,機(jī)組振動就要發(fā)生變化。由于熱慣性,后者引起的振動變化在時間上要比負(fù)荷的改變滯后得多。若試驗(yàn)結(jié)果表明,振動隨負(fù)荷的增大立即增大,則說明振動與傳遞的扭矩有關(guān),一般是聯(lián)軸節(jié)有缺陷或齒牙之間負(fù)荷不均等原因造成的。負(fù)荷試驗(yàn)時負(fù)荷的增加應(yīng)在運(yùn)行規(guī)程允許的范圍內(nèi)進(jìn)行。試驗(yàn)時應(yīng)保持真空等參數(shù)不變。
The purpose of the load test is to determine the impact of changes in the mechanical and thermal states of the steam turbine on vibration during the load change process of the unit. When the load of the unit changes, on the one hand, the torque transmitted by the turbine through the coupling to the generator will immediately change. If the coupling is defective, the vibration state of the unit will also change immediately. On the other hand, changes in steam flow through the turbine can cause changes in steam pressure and temperature distribution inside the cylinder, which means that the thermal expansion of the turbine cylinder, rotor, and bearing seat needs to be correspondingly changed. If the cylinder undergoes uneven deformation at this time, causing the rotor center to be misaligned, resulting in defects such as bearing failure or jamming of the cylinder sliding pin system, the vibration of the unit will change. Due to thermal inertia, the vibration changes caused by the latter are much delayed in time compared to the changes in load. If the test results indicate that the vibration increases immediately with the increase of load, it indicates that the vibration is related to the transmitted torque, usually caused by defects in the coupling or uneven load between teeth. The increase in load during load testing should be carried out within the allowable range of operating regulations. During the test, parameters such as vacuum should be kept constant.
負(fù)荷改變后振動迅速改變,振動變化與負(fù)荷變化之間沒有滯后。
After the load changes, the vibration changes rapidly, and there is no lag between the vibration changes and the load changes.
有的機(jī)組并網(wǎng)或解列時,振動也會發(fā)生較大變化。這種現(xiàn)象說明振動與轉(zhuǎn)子熱變形無關(guān)。主要是由于變負(fù)荷過程中,作用在轉(zhuǎn)子上的力或力矩發(fā)生了變化,導(dǎo)致轉(zhuǎn)子上的激振力發(fā)生了變化。激振力改變后,振動隨即改變。
When some units are connected to the grid or disconnected, the vibration will also undergo significant changes. This phenomenon indicates that vibration is not related to the thermal deformation of the rotor. Mainly due to changes in the force or torque acting on the rotor during the variable load process, resulting in changes in the excitation force on the rotor. After the excitation force changes, the vibration immediately changes.
齒式聯(lián)軸器磨損后間隙變大,機(jī)組升負(fù)荷過程中可能會因傳遞扭矩的變化導(dǎo)致齒套偏向一側(cè)而產(chǎn)生不平衡振動。負(fù)荷變化、傳遞扭矩變化、齒套偏移、不平衡力變化、振動變化五者之間幾乎是同步的。
After the wear of the gear coupling, the gap increases, and during the load increase process of the unit, there may be unbalanced vibration caused by the deviation of the gear sleeve to one side due to changes in torque transmission. The changes in load, transmitted torque, gear sleeve offset, unbalanced force, and vibration are almost synchronous.
加負(fù)荷過程中,由于蒸汽流量的增大,汽流激振力越來越大。對于穩(wěn)定性較差的機(jī)組,當(dāng)汽流力增大到一定程度后,會造成機(jī)組失穩(wěn)。此時,振動也會隨負(fù)荷的增加而突然增加。
During the loading process, due to the increase in steam flow rate, the steam flow excitation force becomes greater and greater. For units with poor stability, when the steam flow force increases to a certain extent, it will cause the unit to lose stability. At this point, the vibration will also suddenly increase with the increase of load.
有些機(jī)組帶負(fù)荷過程中,由于傳遞扭矩和部分進(jìn)汽度的變化,轉(zhuǎn)軸在軸瓦內(nèi)的位置會發(fā)生一定變化。如果軸承內(nèi)更小油膜間隙過小,將會導(dǎo)致轉(zhuǎn)軸與烏金之間的輕微摩擦和不穩(wěn)定振動。這種振動將隨負(fù)荷的增加而快速增加。
During the loading process of some units, the position of the shaft inside the bearing pad may undergo certain changes due to changes in transmitted torque and partial steam admission. If the minimum oil film clearance inside the bearing is too small, it will cause slight friction and unstable vibration between the shaft and the black metal. This vibration will rapidly increase with the increase of load.
負(fù)荷改變初期振動變化較小,一段時間后振動逐漸變化,振動變化滯后于負(fù)荷變化。
The initial vibration change during the load change is relatively small, but after a period of time, the vibration gradually changes, and the vibration change lags behind the load change.
這種現(xiàn)象說明振動與膨脹不暢或熱變形等因素有關(guān)。負(fù)荷改變后,汽缸及轉(zhuǎn)子內(nèi)部溫度場發(fā)生了變化,機(jī)組有可能因此而產(chǎn)生膨脹不暢或熱變形故障。前者改變了支承剛度,后者改變了轉(zhuǎn)子上的激振力,都會導(dǎo)致振動的變化。由于溫度變化以及由此引起的熱變形和膨脹等都需要時間,因此出現(xiàn)這類故障后,振動變化大多滯后于負(fù)荷變化。
This phenomenon indicates that vibration is related to factors such as poor expansion or thermal deformation. After the load changes, the temperature field inside the cylinder and rotor changes, which may result in poor expansion or thermal deformation faults in the unit. The former changes the support stiffness, while the latter changes the excitation force on the rotor, both of which can lead to changes in vibration. Due to temperature changes and the resulting thermal deformation and expansion, which require time, vibration changes often lag behind load changes after such faults occur.
檢查機(jī)組膨脹是否正常,可根據(jù)汽缸兩側(cè)膨脹指示器或自行架設(shè)百分表來分析。如果兩側(cè)指示相同,但數(shù)值偏小,說明汽缸膨脹不暢;如果兩側(cè)指示值差異較大,說明汽缸存在跑偏。汽缸膨脹不暢或跑偏主要是由于汽缸及所屬管道較重、汽缸受管道約束力較大、軸承座與臺板之間缺少潤滑或潤滑油脂干枯、汽缸剛性不足等因素所引起的。這時應(yīng)力求減少汽缸膨脹阻力和管道約束力,增強(qiáng)汽缸剛度,延長暖機(jī)時間。
Check whether the expansion of the unit is normal, and analyze it based on the expansion indicators on both sides of the cylinder or by setting up a dial indicator on your own. If the indications on both sides are the same, but the values are too small, it indicates that the cylinder is not expanding smoothly; If there is a significant difference in the indicated values on both sides, it indicates that the cylinder has deviated. The poor expansion or deviation of the cylinder is mainly caused by factors such as the cylinder and its associated pipeline being heavy, the cylinder being heavily constrained by the pipeline, the lack of lubrication or dry lubricating grease between the bearing seat and the bedplate, and insufficient rigidity of the cylinder. At this point, efforts should be made to reduce cylinder expansion resistance and pipeline restraint, enhance cylinder stiffness, and extend warm-up time.
圖片
picture
變化真空試驗(yàn)
Variable vacuum test
大型汽輪機(jī)低壓轉(zhuǎn)子軸承通常與排汽缸連成一個整體。凝汽器內(nèi)建立真空時,在大氣壓力作用下,排汽缸和位于其上的軸承座會下沉。真空變化的過程中,排汽缸溫度也會發(fā)生變化,這些因素都會影響振動。真空試驗(yàn)的目的在于判別機(jī)組振動與真空及排汽溫度之間的關(guān)系,也可用于判斷汽缸底部與臺板之間的接觸狀態(tài)。
The low-pressure rotor bearings of large steam turbines are usually connected to the exhaust cylinder as a whole. When a vacuum is established in the condenser, the exhaust cylinder and the bearing seat located on it will sink under the action of atmospheric pressure. During the process of vacuum change, the temperature of the exhaust cylinder will also change, and these factors will affect vibration. The purpose of vacuum testing is to distinguish the relationship between unit vibration, vacuum, and exhaust temperature, and can also be used to determine the contact state between the bottom of the cylinder and the bedplate.
真空試驗(yàn)通常是在較低負(fù)荷下進(jìn)行,這時真空變化范圍可以大些。真空變化可以通過改變凝汽器循環(huán)水量來完成。真空改變后,應(yīng)立即測取振動值,穩(wěn)定半小時后再測一次振動。
Vacuum tests are usually conducted at lower loads, where the range of vacuum changes can be larger. The vacuum change can be achieved by changing the circulating water volume of the condenser. After the vacuum changes, the vibration value should be measured immediately, and after stabilizing for half an hour, the vibration should be measured again.
振動隨真空的變化而迅速變化
Vibration rapidly changes with changes in vacuum
這種情況多出現(xiàn)在排汽口與凝汽器采用彈性連接的機(jī)組上。主要原因有,排汽缸剛度較差、軸承座標(biāo)高變化影響對中偏差;真空變化過程中,低壓缸動靜部分間隙變化較大并導(dǎo)致了摩擦;排汽缸底部與臺板之間接觸不好。真空變化過程中因排汽缸位置變化,導(dǎo)致排汽缸底部與臺板之間出現(xiàn)松動和支承系統(tǒng)剛度降低。
This situation often occurs in units where the exhaust port and condenser are elastically connected. The main reasons are that the stiffness of the exhaust cylinder is poor, and changes in the elevation of the bearing seat affect the alignment deviation; During the vacuum change process, the gap between the dynamic and static parts of the low-pressure cylinder changes significantly, leading to friction; Poor contact between the bottom of the exhaust cylinder and the bedplate. During the vacuum change process, due to changes in the position of the exhaust cylinder, there is looseness between the bottom of the exhaust cylinder and the bedplate, and the stiffness of the support system decreases.
振動變化滯后于真空變化
Vibration changes lag behind vacuum changes
振動變化滯后于真空變化,表明振動與熱狀態(tài)有關(guān),這是因?yàn)檎婵兆兓倪^程中,排汽缸溫度也發(fā)生了變化。這種情況多發(fā)生在排汽口與凝汽器采用剛性連接、且排汽部分剛度又較好的機(jī)組上。
The vibration change lags behind the vacuum change, indicating that the vibration is related to the thermal state. This is because during the process of vacuum change, the temperature of the exhaust cylinder also changes. This situation often occurs in units where the exhaust port and condenser are rigidly connected, and the exhaust part has good stiffness.
軸承潤滑油試驗(yàn)
Bearing lubricating oil test
軸承工作狀況對于旋轉(zhuǎn)機(jī)械安全運(yùn)行至關(guān)重要。軸承間隙過大、供油不足、油溫不當(dāng)、載荷過重或過輕等都會使軸承發(fā)生故障。改變軸承潤滑油溫和壓力,也就改變了軸承工作狀態(tài)。通過該試驗(yàn),可以分析軸承工作狀況及其對振動的影響。
The working condition of bearings is crucial for the safe operation of rotating machinery. Excessive bearing clearance, insufficient oil supply, improper oil temperature, heavy or light load can all cause bearing failure. Changing the temperature and pressure of the bearing lubricating oil also changes the working state of the bearing. Through this experiment, the working condition of the bearing and its impact on vibration can be analyzed.
潤滑油壓試驗(yàn)時,可以先將油壓升高20~40kPa,觀察振動是否因軸承供油量的增大而發(fā)生變化。如果振動是由于軸承供油不足而引起的,那么供油壓力提高后,振動幅值將明顯變小。
During the lubrication oil pressure test, the oil pressure can be increased by 20-40kPa to observe whether the vibration changes due to the increase in bearing oil supply. If the vibration is caused by insufficient oil supply to the bearing, the amplitude of the vibration will significantly decrease as the oil supply pressure increases.
油溫試驗(yàn)可以在高和低兩種狀態(tài)下進(jìn)行。油溫改變后,需要立即測量振動。穩(wěn)定30min后再次測量振動。油溫降低過程中,處于穩(wěn)定性邊緣的軸承有可能發(fā)生油膜振蕩,振動突增。試驗(yàn)中一旦出現(xiàn)這種趨勢,應(yīng)立即停止試驗(yàn)。
The oil temperature test can be conducted in both high and low states. After the oil temperature changes, it is necessary to immediately measure the vibration. Measure the vibration again after stabilizing for 30 minutes. During the process of decreasing oil temperature, bearings at the edge of stability may experience oil film oscillation and sudden increase in vibration. Once this trend occurs during the experiment, the experiment should be stopped immediately.
本文的精彩內(nèi)容由沼氣發(fā)電機(jī)組提供知識提供,本網(wǎng)站還有很多的精彩內(nèi)容,更多的內(nèi)容您可以點(diǎn)擊進(jìn)入:http://m.elmasticar.com我們有專門的客服為您解答問題
The exciting content of this article is provided by the knowledge of biogas generator units. There are also many exciting content on this website, and you can click to enter more content: http://m.elmasticar.com We have dedicated customer service to answer your questions